Fuel Oil Viscosity Controller Working Principle
Basic Principle of Viscosity Controller
The basic principle of the Viscotherm viscosity monitoring device or viscosity controller is shown in the figure below. A continuous sample of the fuel is pumped at a constant rate through a fine capillary tube. As the flow through the tube is laminar, pressure drop across the tube is proportional to viscosity.
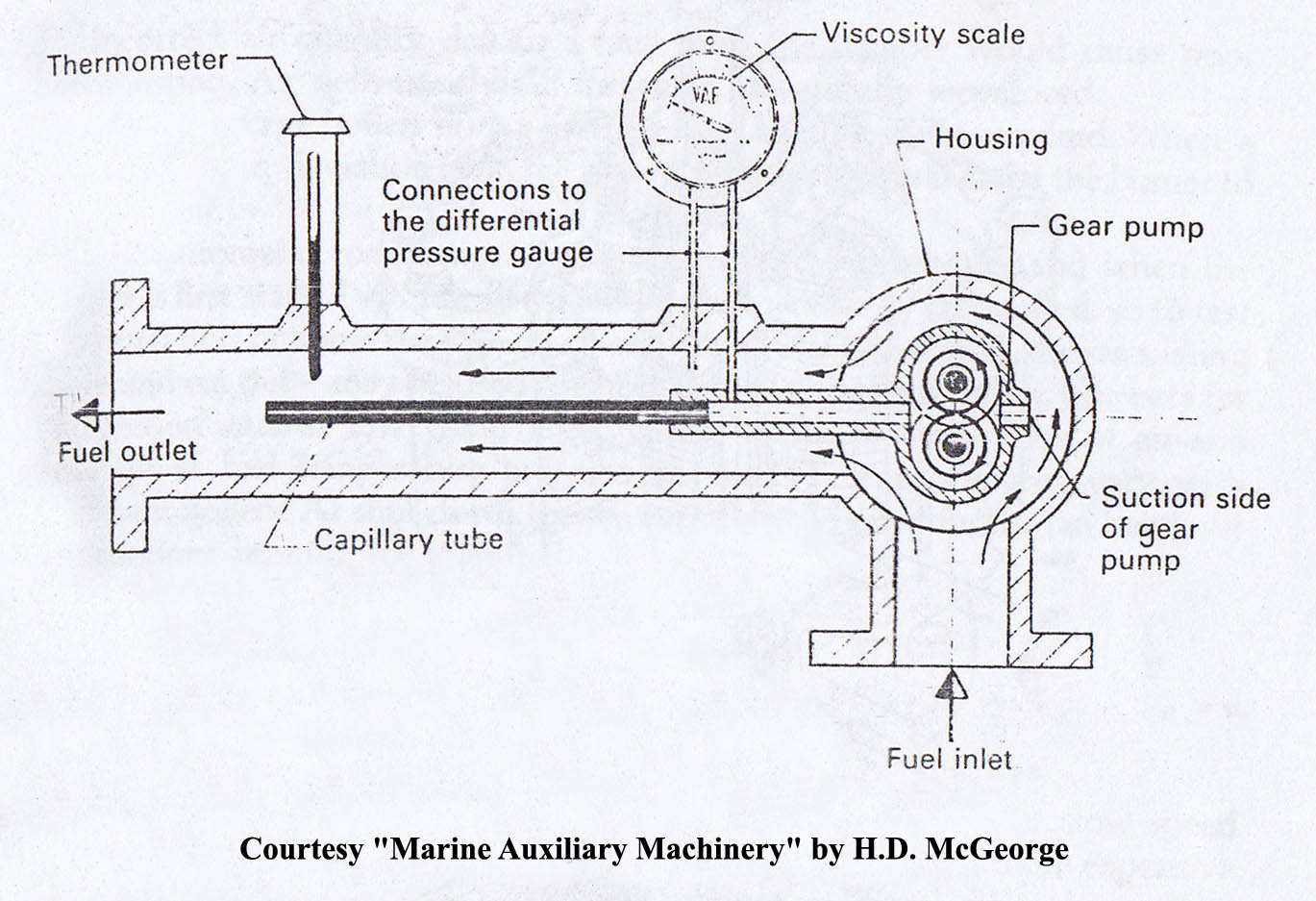
In this viscosity controller unit an electric motor drives the gear pump through a reduction gear at a speed of 40 rpm. The pump is positioned in the chamber through which fuel is passing from the heater to the fuel pumps or combustion equipment. Tapping points are provided to enable the pressure difference to be measured by means of a differential pressure gauge. The gauge is calibrated directly in terms of viscosity. Parts in contact with the fuel are of stainless steel for corrosive resistance.
A differential pressure transmitter shown below provides an analogue of viscosity to a pneumatic controller, which regulates the supply of fuel heating steam through a control valve.
References
“REED’S GENERAL ENGINEERING KNOWLEDGE FOR MARINE ENGINEERS”, by Leslie Jackson and Thomas D. Morton