What is Net Positive Suction Head or NPSH
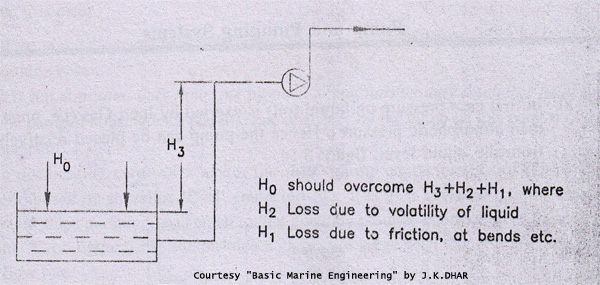
From the figure shown, If pressure exerted by atmospheric air (or any other atmosphere, which is surrounding the liquid on suction side) is H0 and is more than the 3 losses mentioned below:
- Loss of head because of friction in suction line, H1
- Loss of head because of volatility of liquid, H2
- Loss of head in rising the liquid into the pump suction, H3
Only then will the liquid rise up to the pump. However the liquid can be discharged effectively and without cavitation of the pump only if this ‘left over head’ called ‘available NPSH (Net Positive Suction Head) is greater than the ‘required NPSH’ of the pump. Former we have calculated as
[H0 – (H1 + H2) + or – H3]
and later is given by pump manufacturer after conducting trials on the pump.
The ‘required NPSH’ curve of a pump is provided by the pump manufacture.
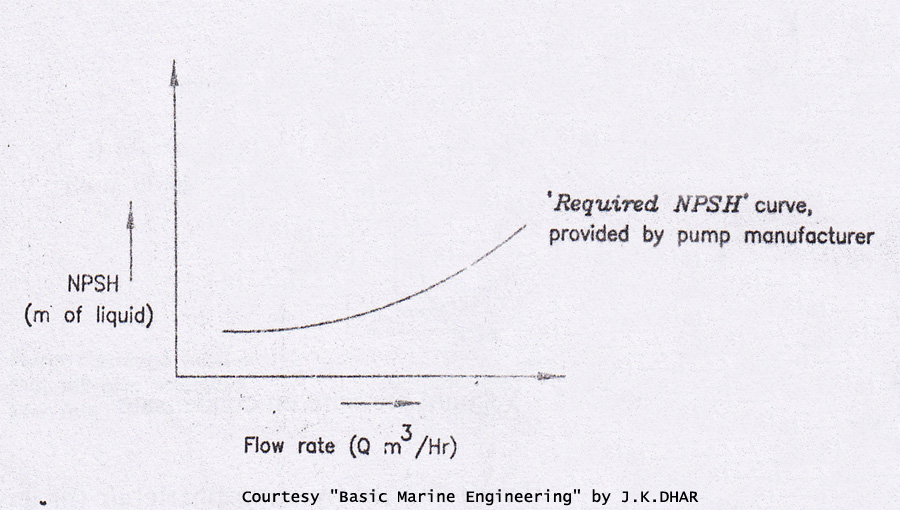
At lesser flow rate the pump requires lesser NPSH. Therefore when an oil tank of a tanker is being stripped; to prevent cavitation and vibration of the pump and yet strip the cargo tank almost dry, we reduce the flow rate of the pump as the level of the liquid falls.
Though now the pump discharges at slow rate but same time it does not cavitate as value of ‘required NPSH’ is much lesser and is easily provided even by he reduced liquid level of tank. Alternatively if ‘available NPSH’ is less than ‘required NPSH’, increasing the inert gas pressure will delay the time when pump will start cavitating.
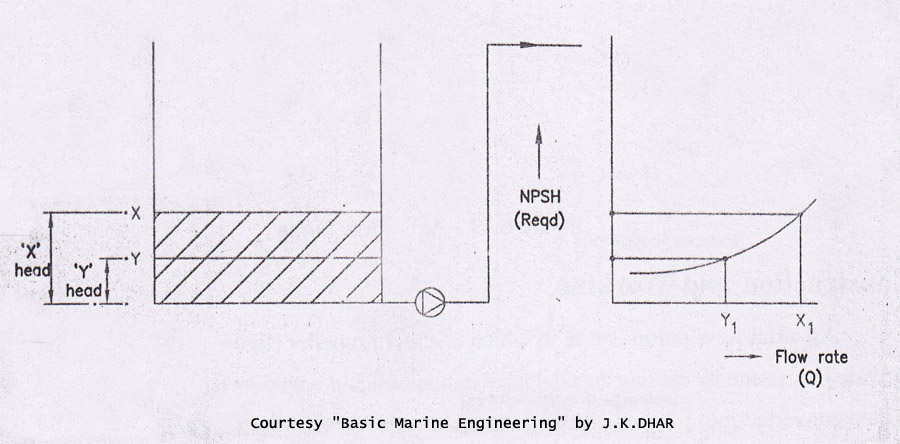
Referring to the figure above, when cargo level in tank is at ‘X’, a flow rate upto ‘X1’ can be maintained without fear of cavitation of the pump. When cargo level drops to say level ‘Y’, the flow rate should be reduced to or below ‘Y1’ to avoid cavitation. In the tankers this is done by throttling the discharge valve of the cargo line.
References
“Basic Marine Engineering” by J.K.DHAR